John Deere: Planting the Digital Seeds of Change
A Look at John Deere’s Digital Transformation
Add bookmark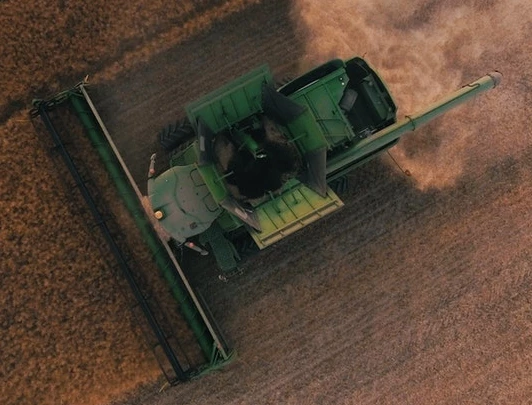
In a sense, John Deere has always been a technology company. In the mid-19th century, the original John Deere engineered the steel plow and revolutionized farming. Over 180 years later, John Deere is shaking up the agricultural industry again by developing a new fleet of AI-powered, autonomous tractors, drones and other farming equipment. As a result, the company has successfully evolved from a high-tech machinery manufacturer to an Agritech innovator.
As with any digital transformation, innovation always begins behind the scenes. Over 25 years ago, John Deere created its Intelligent Solutions Group (ISG), an internal innovation hub consisting of data scientists and software engineers. The goal of this team was to develop and roll out advanced technology solutions and processes across the business. In addition, back in 2017, John Deere acquired Blue River Technology, a company that develops artificial intelligence (AI) and computer vision solutions to power autonomous agricultural robots.
Over the past 3 years, John Deere has also successfully transformed its IT organization to make it more agile and project-based. They also created a comprehensive training program designed to amplify its investments in agile.
As Ganesh Jayaram, John Deere's VP of information technology, recently explained in an interview with Bain & Company, “So we have two physical dojo spaces. We call them the Foundry. And it's an immersion area that we bring product teams to learn both Agile practices as well as technical practices from our coaches that are housed in the Foundry. The second thing that we did was to take these teams through immersion. So every time they come in, it's about 90 days of immersive training with our coaches in the Foundry.”
Smart Connected Equipment
When it comes to pioneering cutting-edge, digitally enhanced farming equipment, John Deere is certainly ahead of the curve. For example, John Deere's highly automated 8RX tractor with a 60-foot, 24-row planter has more than 300 IoT sensors and 140 controllers, which can process 15,000 measurements per second per machine.
Using the technology developed by Blue River, John Deere has also developed an autonomous “See and Spray” system. This new tool uses 97 “robots” to identify and spray weeds with great precision, reducing herbicide use by 80-90%. As a result, farmers not only save money but, as they no longer accidentally kill as many primary crops, it also increases overall productivity. In fact, early tests on cotton plants showed that production can double.
John Deere’s farming analytics tool, JDLink™ Connect telematics, combines agronomic (crop management) data, machine operation data (e.g., fuel levels, run time, engine RPM) and external data (e.g., weather prediction data, commodity pricing, supplier data and even data from other farmers) to deliver decision-enhancing insights regarding both crop production and predictive maintenance of equipment.
As HBR puts it, JDLink enables farmers to “monitor activity in real-time, analyze performance, determine how best to utilize equipment, and collaborate with partners for insights and ‘prescriptions’ using algorithms that help the farmer decide what to plant, where and when with optimized conditions.”
Smart Connected Factories
The proliferation of intelligent farming equipment has enabled John Deere to develop a bleeding-edge approach to manufacturing centered on data analytics and advanced automation.
In November 2020, the company announced it would be investing $546,000 for five CBRS Priority Access Licenses to fuel its 5G and manufacturing 4.0 ambitions. As Jahmy Hindman, chief technology officer at John Deere, told Enterprise IoT insights, “Our focus on tech goes way beyond the fields. It impacts every aspect of our business… Implementing 5G in our manufacturing facilities allows John Deere to make significant progress in our Smart Industrial strategy by turning factories into smart and connected manufacturing facilities – a critical piece of the industrial IoT.”
In addition to powering a new suite of high performance computing analytics (a.k.a. “big data”), this private 5G technology will enable the adoption of edge computing and autonomous devices as well as a larger set of smart applications like real-time location systems, asset tracking, inventory management, wearables, production automation and robotics.
“One of the top goals that we continue to have going forward is just smart, connected factories and smart, connected supply chains making us a very nimble and efficient and technical savvy company,” Craig Sutton, John Deere’s manager of manufacturing innovation and technology strategy, told ForConstructionpros.com. “It's a very, very tech savvy environment that we have going on inside our factories. We have digital twins, we have digital models, we have paperless work instructions. We have automation that's been in place and we continue to expand, and we see 5G continue to enable that, give us more opportunities to bring in machine learning inside a factory and augmented reality and how those technologies are going to continue to really drive our efficiencies.”
Want content and event updates in real-time? BECOME AN INTELLIGENT AUTOMATION NETWORK (IAN) MEMBER