Kemira’s Profitable Digital Transformation
A Roadmap for Linking Digital Maturity to Revenue Growth
Add bookmark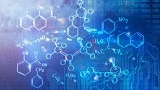
Though not a household name, chances are you’ve come into contact with a product that required the use of Kemira Oyj’s chemical solutions to create. As a global producer of chemical solutions for water-intensive industries, Kemira’s products are used for everything from paper & pulp production to treating drinking water.
In recent years, Kemira has embraced digital transformation as a means to not only increase profitability, but business resilience and environmental sustainability as well. Here’s a look at a handful of their initiatives.
Industry 4.0
Over the past decade, Kemira has invested heavily in automating its manufacturing processes both to increase productivity and minimize waste - a central component to Kemira reaching its sustainability goals.
For example, Kemira recently partnered with Siemens to overhaul one of its acrylamide and polyacrylamide producing factories. Leveraging Siemens’ distributed control system (DCS), SIMATIC PCS 7, for plant automation, the facility in question was able to not only automate the complete production process but also increase the rate of production by 50%.
In addition, they also partnered with SAP to automate demand planning and forecasting across 60 manufacturing sites and 200 inventories. As a result of this initiative, they were able to eliminate supply gaps and reduce both stock-outs and aging inventory by 50% while also achieving full, end-to-end supply chain visibility.
However, Kemira’s embrace of automation doesn’t stop on the factory floor. In recent years, they’ve also leveraged robotic process automation (RPA) to automate dozens of transactional business processes. In a case study published by their partner in this endeavor, Kofax, Markus Katila, Director of Finance Development at Kemira explained, “The increased automation delivered by Kofax RPA has enabled us to give back around 5,000 hours annually to our finance teams. Additionally, robotics has enabled new processes which were not possible earlier due to huge amounts of manual work.”
Global HR Transformation
Until 2009, Kimera’s HR department, which manages roughly 5,000 employees across 37 countries, was largely decentralized and paper-driven. However, starting with the initial implementation of SAP SuccessFactors 12 years ago, the HR team has undergone quite the transformation.
To augment its initial HRM investment, they also implemented UKG’s HR Service Delivery platform - a tool that included both an employee file management solution and an HR case management application. As a result, they were able to provide users access to key personnel documents from the central employee portal.
In a recent interview with diginomica, Kemira’s Director of Digital HR and Workplace Development, Mirka Janhonen, explained, “Our HR team now has more time to focus on our people and other business-critical tasks to move the organization forward. This solution has given local HR managers the ability to upload, manage, and access employee documentation, as well as templates and other useful information-in fact to date, 25,000 documents and over 100 request forms available for employees to use have been uploaded. The system also automates workflow, so that employee requests are routed to the right person.”
Digital ROI Realized
For many organizations, the ultimate end goal of digital transformation is to not only reduce overhead costs by increasing operational efficiency, but also develop new, digital-first revenue streams. With KemConnect™, Kemira did just that.
Leveraging its heaps of operational data and expertise, Kemira was able to branch out beyond manufacturing physical chemicals to create a digital solution designed to “run patented control algorithms that continuously optimize process conditions in terms of chemistry application.” In other words, it helps Kemira customers automate and optimize the water treatment lifecycle - from sampling to dosing to retrospective tests.
In addition, they’ve also recently launched Predictive Wet End, an explainable AI solution that predicts and prevents issues with paper and board quality and paper machine runnability. Ad Juha Rintala, Manager, Digital Applications Development at Kemira elaborated in a recent press release, “The service allows our customers to see previously unseen events in the process health that impact the quality of the product, hours into the future. It also helps them to understand where the disturbances are originating from, making it possible to prevent e.g. off-spec production”